Vacuum Casting & Silicon Molding
Vacuum casting is used for materials that cannot be cut from or carved out of an original block of material. After making an initial pattern, a silicone mold is made based on the pattern. This allows the desired material to be casted (poured into pattern cavity and hardened). This method allows for the prototyping of clear plastics and rubber parts. Normally, a vacuum casted mold is good for approximately 10-15 pieces.
WB Engineering Company, based in Miami, Florida, likely offers professional vacuum casting and silicone molding services. Vacuum casting is a versatile manufacturing process that involves creating multiple copies of a prototype or part using silicone molds. This method is ideal for producing small to medium production runs with high-quality details and intricate designs.
Silicone molding, on the other hand, is a technique used to replicate objects by creating a flexible mold from a master pattern. This process is known for its ability to produce detailed and complex shapes, making it suitable for various industries, including product design, automotive, and aerospace.
Photos
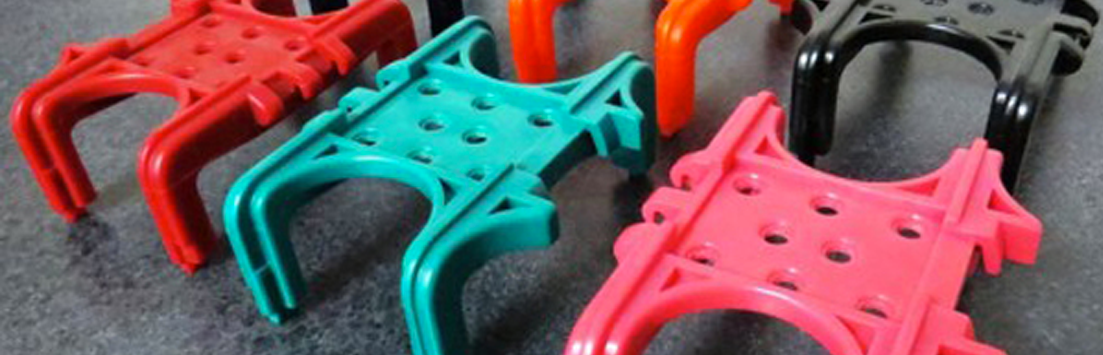
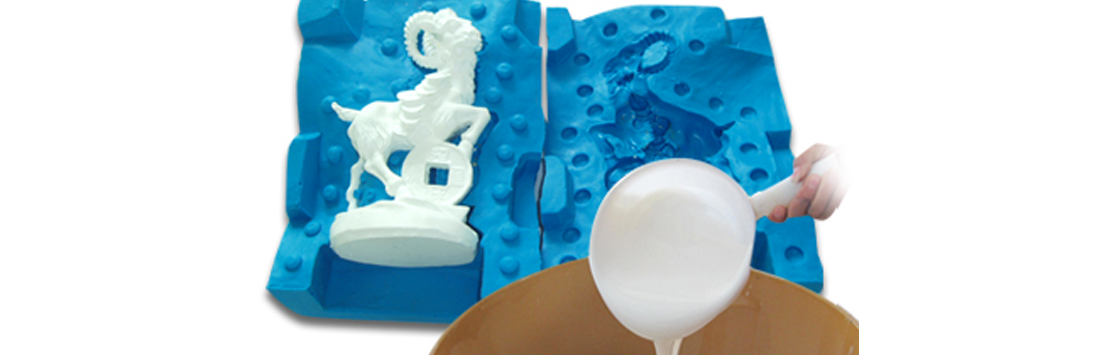
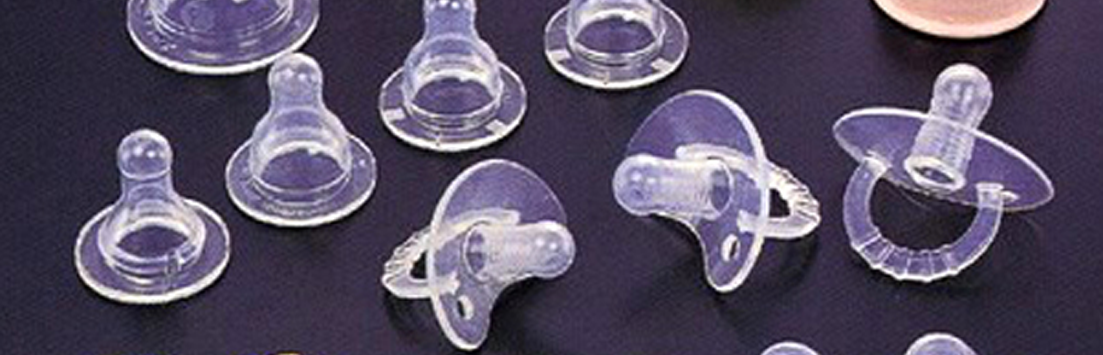
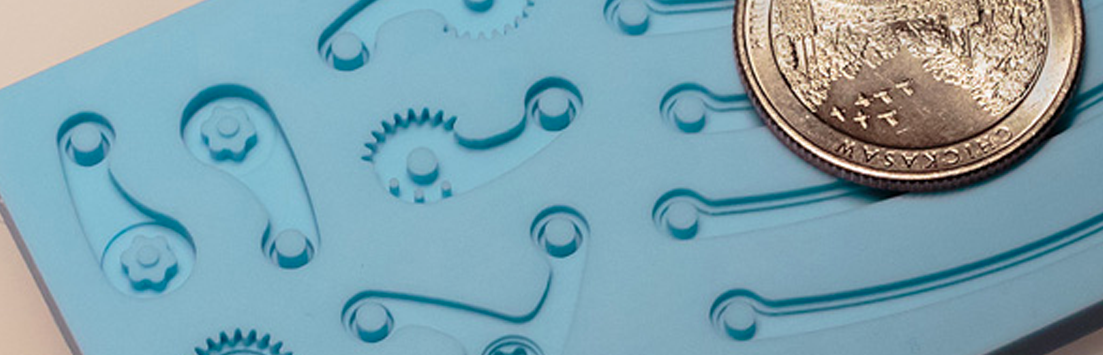
Vacuum Casting and silicone molds are perfect for short run production. Vacuum castings produce prototypes that are precise replicas of the mold that are also dimensionally and texturally accurate. The process starts by placing a two piece silicone mold in a vacuum chamber. The raw material is poured into the mold. The vacuum process draws the liquid into the mold to create the shape. The casting is then cured in an oven, the mold is removed, and the casting is complete!
WB Engineering Company in Miami, Florida, stands at the forefront of cutting-edge manufacturing services, specializing in vacuum casting and silicone molding. With a commitment to excellence, they offer a comprehensive range of solutions to meet the diverse needs of their clients. Whether you are in the product design phase, require low-volume production, or need intricate parts replicated, WB Engineering Company brings a wealth of expertise to the table.
The vacuum casting process employed by WB Engineering Company ensures the creation of high-quality prototypes and end-use parts. By utilizing silicone molds, they enable the production of detailed and finely finished components, making it an ideal choice for industries where precision and intricacy are paramount. This method is not only cost-effective but also expedites the product development cycle, providing clients with efficient and reliable solutions.
In addition to their technical proficiency, WB Engineering Company places a strong emphasis on customer collaboration. Their team works closely with clients throughout the project lifecycle, from initial design discussions to the delivery of the final product. This collaborative approach allows for customization, ensuring that the unique requirements of each project are met with precision. With WB Engineering Company’s vacuum casting and silicone molding services, clients can expect a seamless and streamlined manufacturing experience, driving innovation and excellence in their respective industries.
Advantages
Vacuum Casting & Silicone Molding can create prototypes that are very detailed without having to create multiple parts. The quality of prototype is very similar to the final product. Prototypes are excellent marketing visuals and can have functional components. Various colors can be used.
Applications
• Industrial design
• Aerospace
• Mechanical
• Commercial
• Consumer products creating molds for short batch production