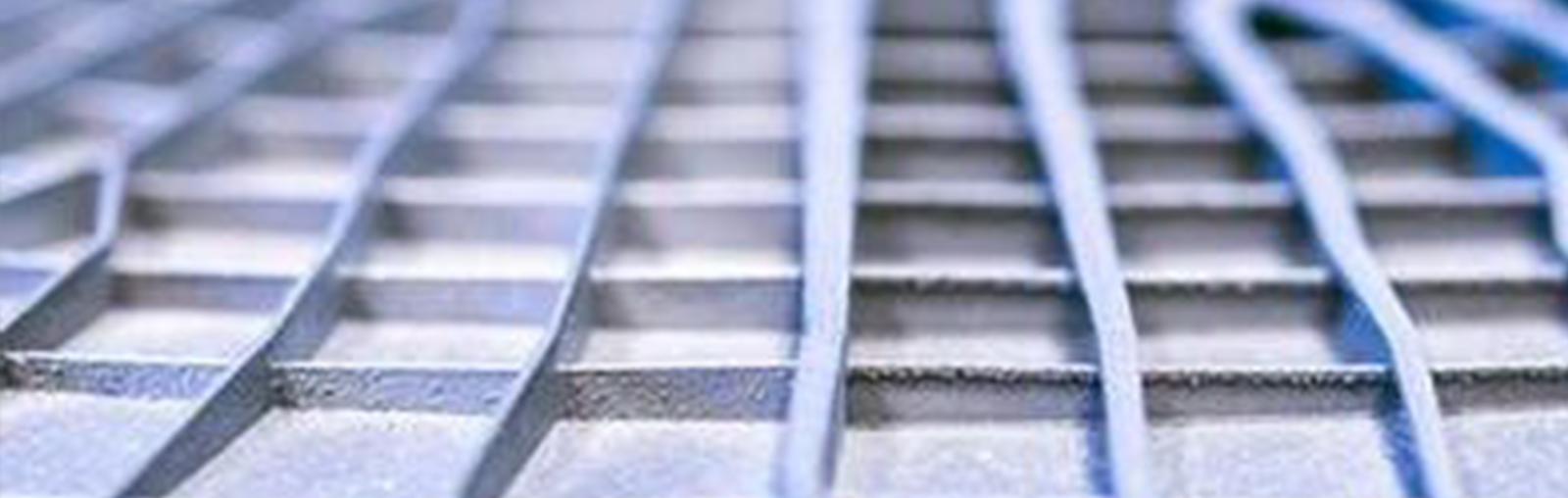
5 Reasons Why Metal 3d Printing Is Big And Getting Bigger
People ask me if and when 3D printing will become a method of mass production. As far as plastics go, I don’t know. For metals, though, it is a whole different story: it is already happening. Metal 3D printing technologies are evolving at breakneck speed, constantly increasing their size and velocity capabilities. One of the reasons for this, in my opinion, is the intense competition, both between different technologies and different approaches to the same technology. This is not, however, the only reason.
Tough Competition
The primary industrial metal 3D printing technology today is powder bed fusion. There are eight (and a half) players currently on the market offering this technology and one (and a half) that is entering it now. That makes 10 players all together. The “half” is German metal manufacturing giant Trumpf, which has entered the market in a joint venture with Italy’s Sisma. These two companies join four more German companies: two are the market leaders EOS and Concept Laser, followed by SLM Solutions and the smaller REALizer.
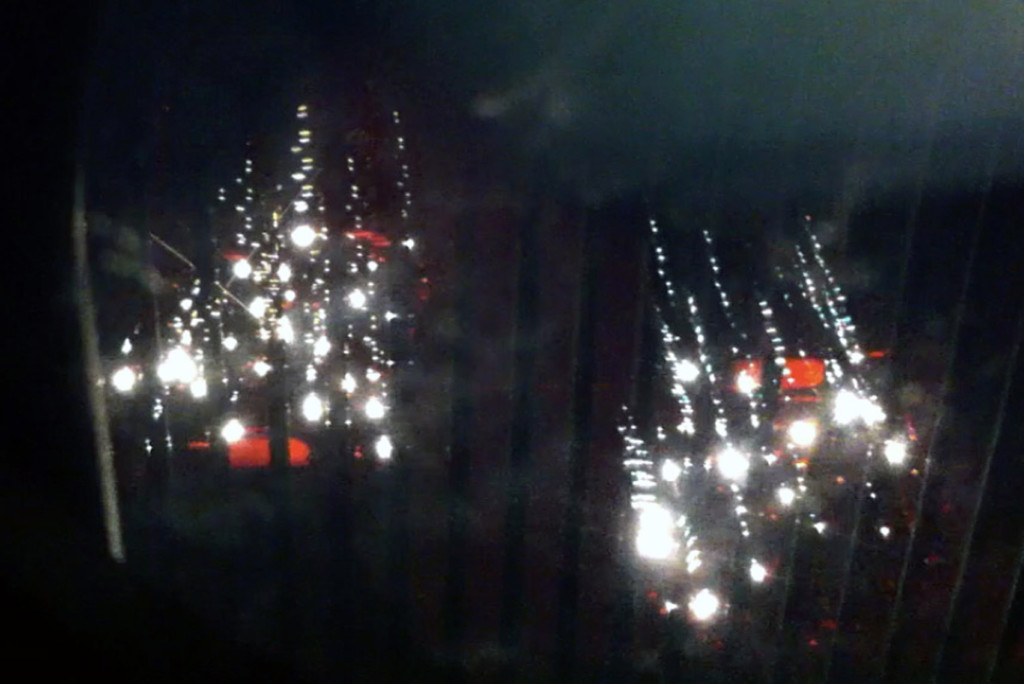
In the UK, the manufacturing giant Renishaw offers a range of very specific SLM 3D printers. There is one company in the US, 3D Systems, which offers metal 3D printers through its acquisition of France’s Phoenix. The new player that just entered the market is Additive Industries from The Netherlands. And there is one company that has taken a different approach: Sweden’s Arcam Metals, with its unique Electron Beam Melting technology. This means that all these companies from some of the world’s most industrialized nations, are competing to offer better and more automated machines and the amazing part is that they still can meet demand. One more player, Aero Sud in South Africa, will soon be entering the market with the biggest metal powder bed fusion 3D printer ever built.
More Technologies
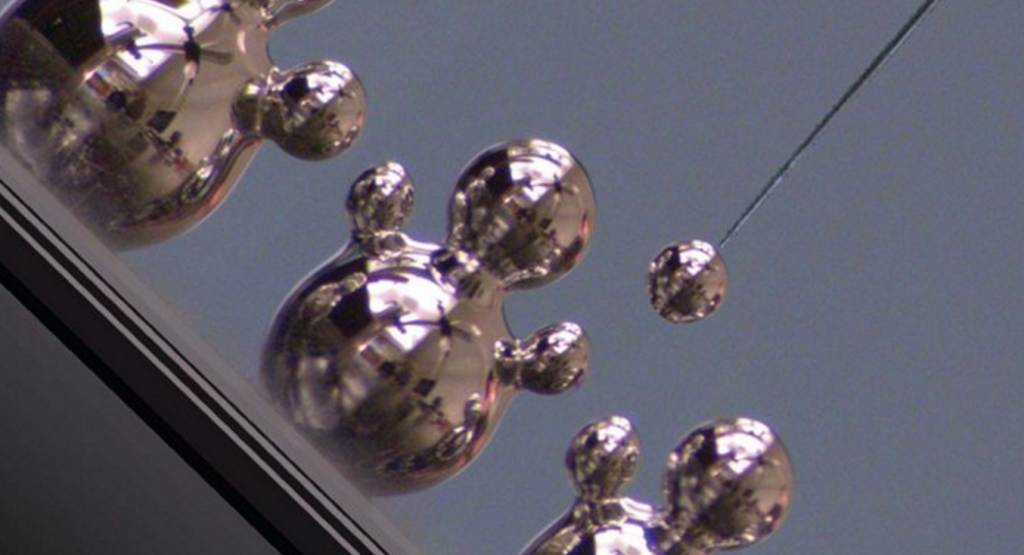
On top of this, there are other technological approaches that are pressing on. For example, the binder jetting technology proposed by ExOne and Digital Metals. Although binder jetting needs post-processing, the technology can do things that powder bed fusion cannot. In the case of Digital Metals, it can create microscopic details and some of the thinnest walls possible with metal. In the case of ExOne, it can create some seriously large parts at affordable costs, as in the recent partnership with Powder Manufacturer Puris. It doesn’t end here, because Israel-based XJet is about to launch a machine capable of injecting nano metal particles. This will open yet unseen possibilities for thin walls, high detail, smooth finish, and fully dense parts that may even be made up of multiple materials in the future.
Bigger Industries
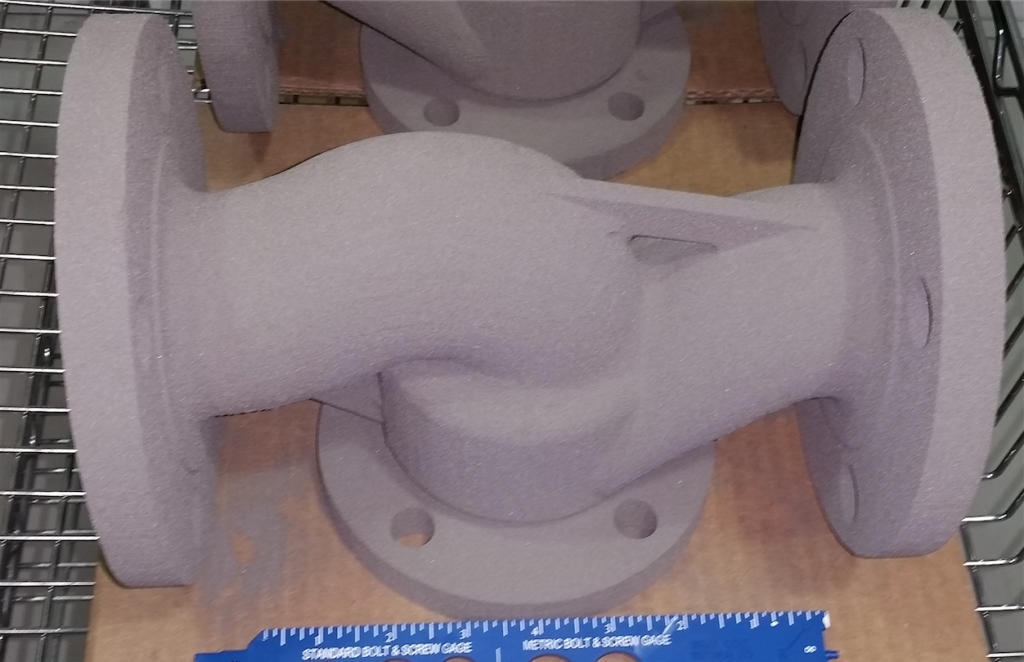
However, all this would not matter if there was no big demand, as industry pioneers know full well. That demand now exists because the aerospace industry is ready to implement it now and the automotive industry will be in a couple of years. Not for prototyping, but for actual production, and the reason is that the additive parts made in metal have comparable properties to the parts manufactured traditionally while adding all of the new geometrical possibilities. In the aerospace industry, the use of topological optimization and generative design is soon going to be a must in order to meet the environmental requirements of tomorrow. Even without the high demand from the defense industry, AM adoption is booming.
Larger Companies
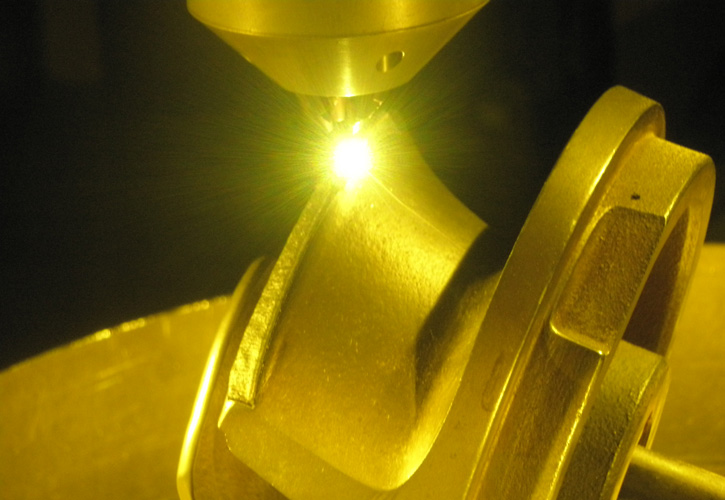
One other technology that can be considered additive manufacturing is also booming: we are talking about Directed Energy Deposition (Aka laser cladding). It is a type of metal deposition, so it does have some geometrical limitations, however it can deposit very large amounts of materials in a short time, which means that it is fast. Furthermore, it can be integrated into multi-tool robotic systems. Giants such as DMG Mori and Trumpf, whose yearly revenue almost equal those of the entire 3D printing industry combined, are starting to seriously push this metal powder based technology. Then, of course, there are also smaller companies that are making big moves, such as Sciaky. The US company’s unique EBAM technology – which is a type of DED only it melts a metal filament with an electron beam instead of powder with a laser – is already being used in the US aerospace and defense industries for very large size parts.
More Materials
The only question that remains is: who feed this demand its the right materials? We’ll explore that in the coming weeks.
Source by https://3dprintingindustry.com