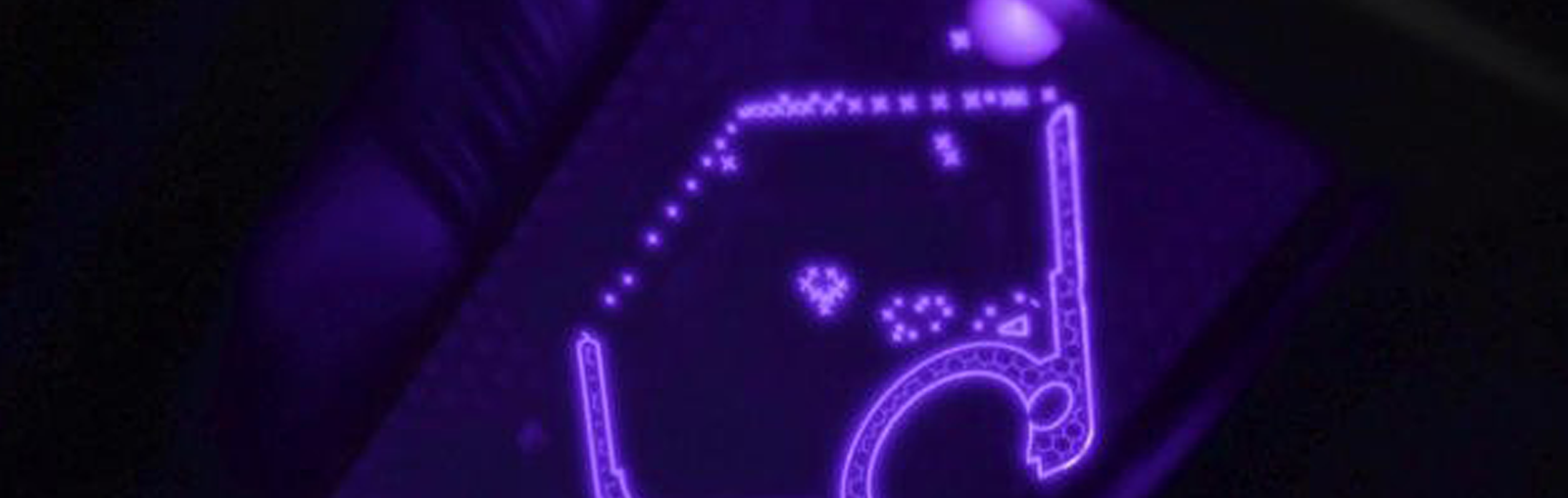
Rapid Part Replacement Ready for Take Off?
Rapid part replacement with Figure 4 technology
As a globally recognized leader in research, development and transition of technologies, the University of Dayton Research Institute (UDRI) is conducting one of three awarded America Makes MAMLS projects under the theme: Emerging Process Technology for Low Criticality Part Families. Specifically, UDRI is exploring “Rapid Part Replacement via Digital Light Processing,” an additive manufacturing process enabled by 3D Systems’ Figure technology. For the purpose of this study, low criticality parts include electrical connectors, knobs, elastomeric grommets, and spacers, each of which serves a functional purpose onboard aircraft.
Both UDRI and 3D Systems also participated in Phases 1 and 2 of the MAMLS program, which were similarly focused on sustainment, but under different core topics. Although each project has been independent from the others, the previous phases laid the groundwork for the third phase to launch without delay and gave UDRI and 3D Systems a practical understanding of how the ALCs work, and what their needs are. Phases 1 and 2 also helped to identify the business cases for additive manufacturing for different parts, shedding light on what can and cannot be easily sourced and where using additive manufacturing makes sense.
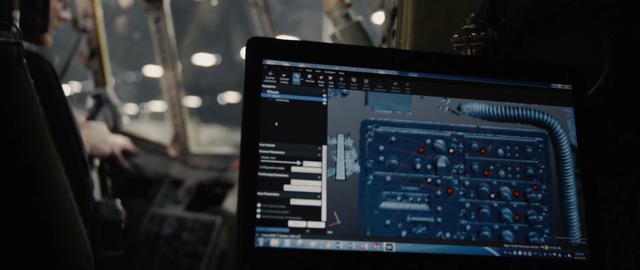
UDRI is digitizing parts to test using a 3D scan-to-CAD workflow.
For legacy aircraft, the business case for additive manufacturing comes into play for parts that are out-of-production due to manufacturing obsolescence, high creation costs, low quantity requirements, unavailability of original tooling, poor documentation, or other availability-related challenges. The speed of part replacement offered by emerging technologies like Figure 4 offers an opportunity to agencies like the U.S. Air Force that can advance strategic sustainment initiatives. Over the next two years of this research project, UDRI and its collaborators will work to uncover where Figure 4 fits into the larger picture of aircraft sustainment.
The need for speed
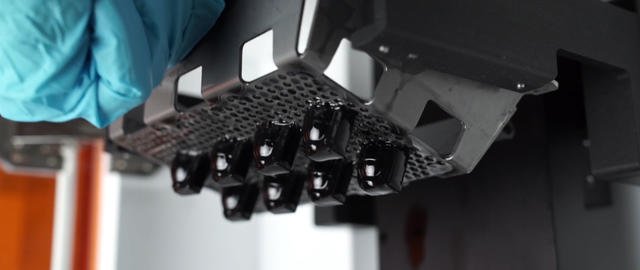
3D Systems’ Figure 4 is a modular manufacturing process that uses a non-contact membrane in combination with a projector-based imaging. In contrast to toolpath-based AM technologies, Figure 4 fabricates an entire part cross-section with a single projection, retaining fine resolution, smooth surfaces, reactive production material chemistries, and fast print speeds. Figure 4 also delivers six sigma repeatability (Cpk > 2) across all Figure 4 materials, making it the most manufacturing ready 3D printing technology available.
Along with geometric accuracy, print speed and material suitability are key. The prospect of performing a lasting custom repair job in a single day is highly appealing to increasing aircraft readiness and availability for same-day mission use. Before that capability can be celebrated however, UDRI is rolling up its sleeves to methodically identify and solve potential issues to pave the way for adoption of Figure 4 technology by the USAF, other DoD (Department of Defense) agencies, and more.
Experts in every corner
UDRI excels in the areas of advanced materials, engineering, aerospace technologies, and structural physics, among others, and is collaborating with external experts to make this project as comprehensive and effective as possible. Together with 3D Systems, UDRI is working through material development, characterization and post-processing protocols to align and document material performance with the requirements of aviation qualified materials. These specifications run the gamut from mechanical and environmental properties to safety standards such as fire retardancy. 3D Systems’ role is to facilitate UDRI by supplying materials for the applications under investigation in this project by either matching existing commercial photopolymers or formulating new ones.
Lockheed Martin and Northrop Grumman are also key collaborators and will perform rigorous inspections on UDRI’s test parts to validate the outcomes. UDRI is going through all the military specifications, ALC, and OEM partner qualifications to test parts against industry standards. According to Dr. Timothy Osborn, Group Leader for Additive Manufacturing Technology Development at UDRI, this assembly of collaborators represents the correct testing matrix to push the research finding into application faster than other programs.
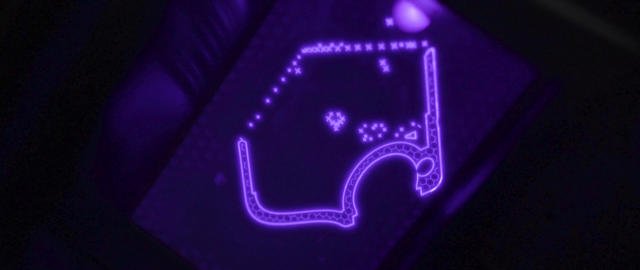
A scientific approach to transitioning digital light processing
The first task of the program will identify the specific parts to test and outline the material specifications those parts require. Using a Creaform HandyScan scanner and reverse engineering software, UDRI will digitize the parts using a 3D scan-to-CAD workflow and prepare the files for printing. Once printed, the material testing will begin. Dr. Osborn predicts the study will begin to generate good data around the six-month mark, culminating in the final report and recommendation to the Air Force upon the project’s completion.
There are currently a number of unknowns around Figure 4 technologies for these applications, but the speed and geometric tolerances of this technology hold significant promise. Through this program UDRI and its collaborators plan to unlock the science required to make rapid part replacement a reality.
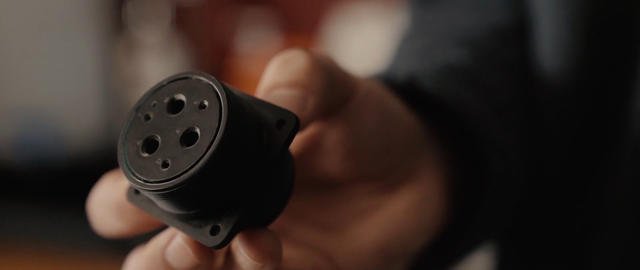
Cleared for public release. Case Number: 88ABW-2018-5721
The sustainment mission of the United States Air Force (USAF) becomes increasingly challenging as large numbers of legacy aircraft, systems and equipment steadily age. Addressing this burden requires quick, reliable and lasting maintenance solutions. Industry frontrunners and researchers are looking beyond traditional sustainment solutions to opportunities in emerging technologies. Rapid part replacement using 3D Systems’ additive manufacturing for built-on-demand inventory control is a compelling solution currently under serious evaluation.
America Makes, the nation’s leading and collaborative partner in additive manufacturing (AM) and 3D printing technology research, discovery, creation and innovation, is at the helm of an initiative to identify and vet nascent sustainment options for transition as appropriate. Under the “Maturation of Advanced Manufacturing for Low-Cost Sustainment” (MAMLS) program, America Makes is now in Phase 3 of a Project Call for applied research and development programs designed to improve efficiency in the factory as well as for Air Logistics Complexes (ALCs) to ensure the strategic readiness of the USAF.
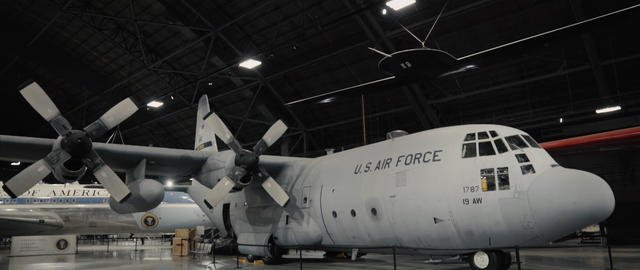
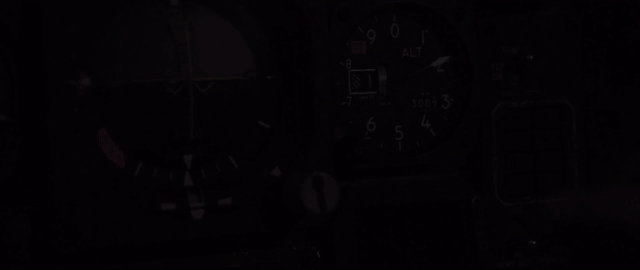
Source https://3dsystems.com