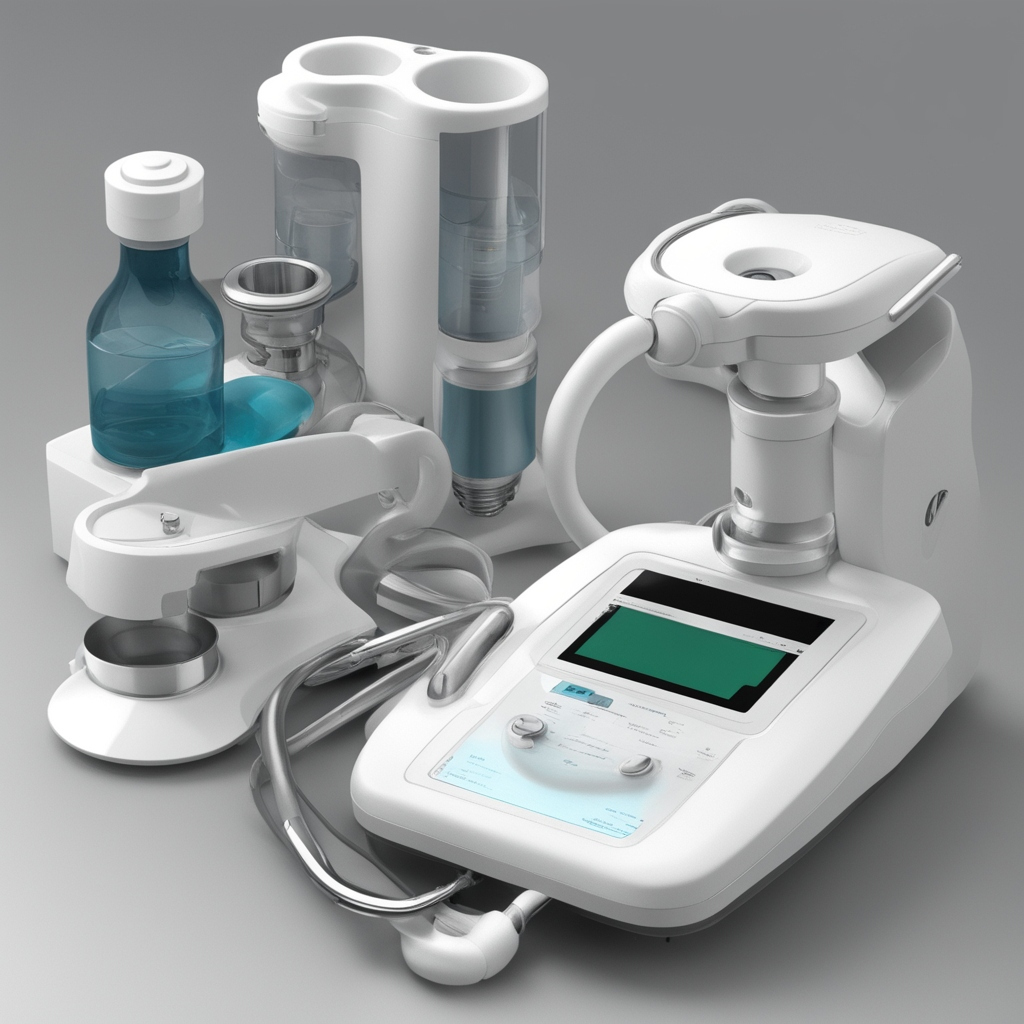
Benefits of 3D printing in the medical devices industry
Customization and Personalization
3D printing allows for the creation of custom-made medical devices tailored to individual patients’ specific needs and anatomy. This is particularly beneficial in orthopedics, dental implants, and prosthetics, where personalized devices can significantly improve patient outcomes.
Rapid Prototyping
With 3D printing, prototypes of medical devices can be produced much faster than traditional manufacturing methods. This accelerates the design process, allowing for quicker iterations and enabling manufacturers to refine and perfect their products in a shorter timeframe.
Complexity Without Additional Cost
Additive manufacturing can create complex geometries that are difficult or impossible to achieve with traditional manufacturing methods. Unlike traditional methods, the cost of 3D printed objects does not increase significantly with complexity, allowing for the design and production of intricate devices without a corresponding rise in price.
Reduced Waste
3D printing is an additive process, building objects layer by layer, which results in significantly less waste material compared to subtractive manufacturing processes like CNC machining. This not only reduces costs but also aligns with sustainable manufacturing practices.
Cost-effective low-volume Production
For small-batch production, 3D printing is more cost-effective than traditional manufacturing methods, which often require expensive molds and setups. This is particularly advantageous for producing bespoke medical devices or for small-scale production runs of innovative new products.
Improved Patient Outcomes
Customized 3D-printed medical devices, such as implants and prosthetics, can lead to better patient outcomes. These devices are designed to fit perfectly with the patient’s body, reducing the risk of rejection and improving functionality and comfort.
Enhanced Surgical Planning
3D printing is used to create detailed anatomical models based on patient-specific imaging data. Surgeons can use these models for preoperative planning and practice, reducing surgery times and improving surgical outcomes.
Innovative Device Design
The flexibility of 3D printing encourages innovation in medical device design. Engineers are not limited by the constraints of traditional manufacturing techniques, enabling the development of devices with new functionalities or improved performance.
On-Demand Manufacturing
3D printing allows for on-demand manufacturing of medical devices, reducing the need for large inventories and enabling quick responses to specific medical needs or emergencies.
Education and Training
3D-printed anatomical models provide valuable tools for medical education and training, offering a realistic and hands-on experience for students and professionals to learn about complex anatomical structures and medical conditions.