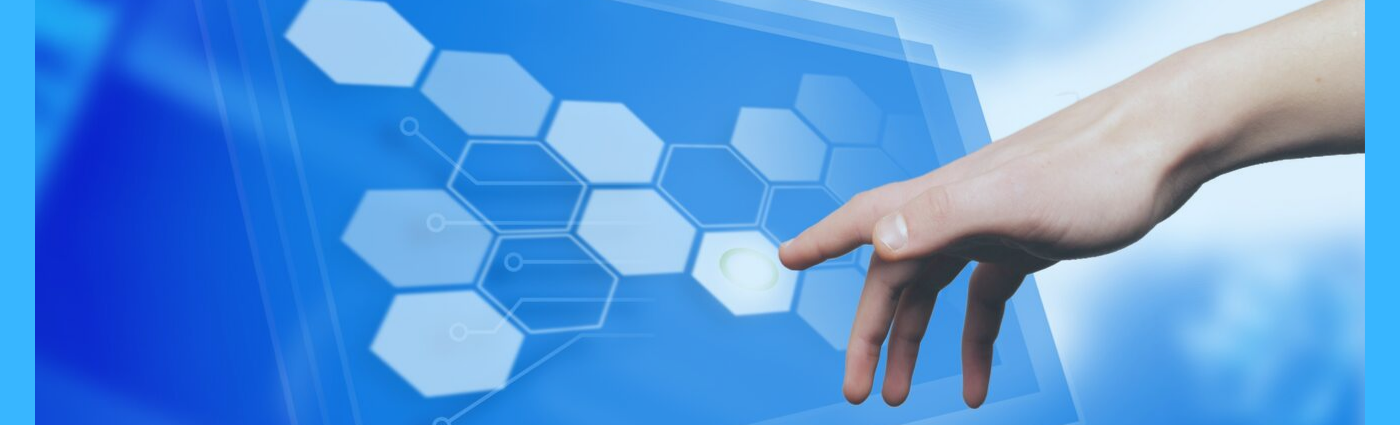
Digital Twin: when and how is it created?
Digital Twin is gaining momentum in manufacturing, aerospace, medical devices, heavy equipment, transportation, and many other industries. Along with innovative Industry 4.0 technologies (cloud computing, additive manufacturing, simulations, IoT, edge computing, big data, analytics, augmented reality), it is transforming the industrial world and the way we design, build, and operate what surrounds us.
For centuries, humans have created machines to perform tasks, accelerate, and improve processes. Now, while Industry 4.0 continues to enable the convergence between the physical and the digital worlds, Digital Twin is here to monitor, optimize, and increase productivity and reliability. And most importantly, it is here to empower workers at all levels of an organization to make more intelligent and educated decisions.
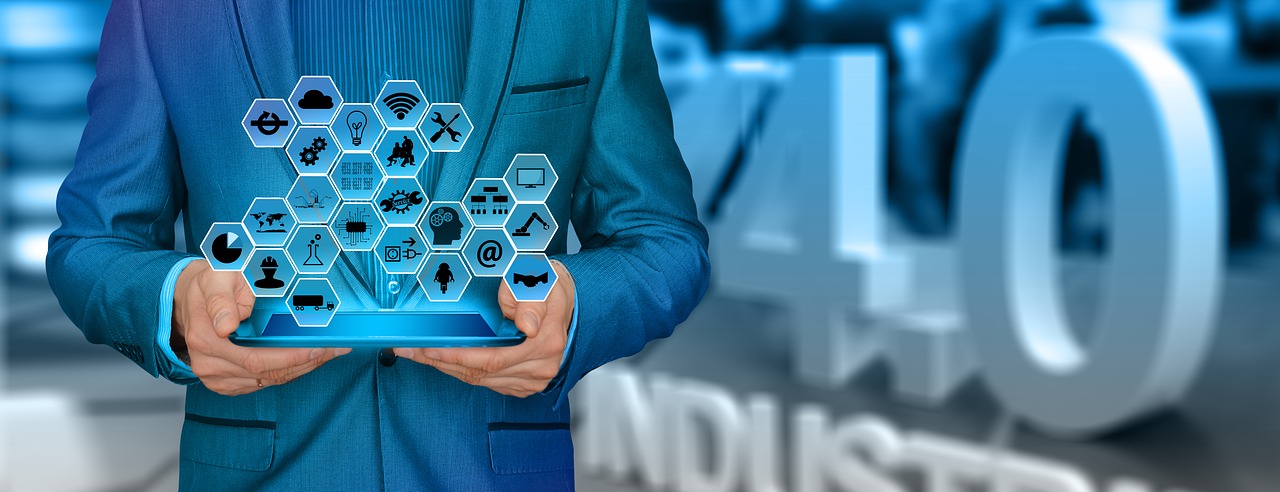
What is a Digital Twin?
A Digital Twin is a virtual replica of a physical product, system, or service. In the case of a product, it looks precisely like its tangible counterpart. It allows analyzing real-world data and real-time monitoring of the physical product even after it has left the factory, and it is operating in the field.
Through sensors embedded in the physical product, the Digital Twin gathers data to give constant insights about the behavior of its Physical Twin. Understanding how production lines are working, preventing accidents, predicting asset downtime, or optimizing next-generation products, all are good examples of the benefits of a Digital Twin.
The Digital Twin is born at the product design and engineering phase as a 3D digital model. It gets developed through technologies such as CAD, CAE, Simulation, and even Generative Design. As this 3D digital model progresses through its product life-cycle journey, it gives way to its Physical Twin. The 3D digital model becomes a product on the manufacturing floor, and later it gets deployed in the field. Thus, fulfilling its purpose as an operational and profitable asset.
How a Digital Twin benefits an organization
As mentioned before, Digital Twin is entering mainstream use among industries. Just now, companies are starting to understand its value.
We can exploit the potential of Digital Twins in many areas. From engineering to customer experience management, the benefits vary depending on the use case. The following are some of them:
- Optimization of existing and next-generation products.
- Cross-Departmental/functional collaboration.
- Reduction of engineering and production costs.
- Operational data presentation in context/role-based.
- Constant insights into the production line and the supply chain.
- Asset Management maximization and optimization.
- Personnel training.
What twin comes first?
The Digital Twin concept has some momentum due to the Industrial Digital Transformation we all are experiencing, and the technologies that encompass the Industry 4.0 stack. Generally speaking, the Digital Twin is a replica of an existing physical counterpart. This would suggest that it comes after its Physical Twin. In a way, this is true. Perhaps that will become clear later on.
The Digital Twin does not exist in a vacuum. For example, you may think of its (physical) twin manifested in an engine, turbine, or even an entire manufacturing plant. Still, those “physical manifestations” were not created from thin air. They first must be digitally designed and engineered.
How Engineering creates a Digital Twin
Long before an actual physical product exists, first comes the creation of a 3D digital model, developed with CAD technology and solid engineering.
This first 3D digital model of a product, ideally, and if it is well designed, will be an exact representation of how the physical product will manifest in the real world. We can argue that we can create a digital model (twin) of a product that has been in service for many years, through 3D scanning, and retrofit it with IoT technology, which is perfectly acceptable. However, we achieve authentic Digital Twin experience only if we design and engineer our products with the right technologies (mechanical, electronic, software, and connectivity). This would allow the 3D digital model to become a genuine Digital Twin sometime down the road on its product life-cycle journey.
The design of the product should be thought to include IoT technology, so this 3D CAD model may become a genuine Digital Twin once its Physical Twin is built and operational, and passes real-time data to its twin. This is the only way these two twins will be a true reflection of each other.
Once the Physical Twin is in operation, the only difference between these two twins should be that the Digital one transcends the walls of the factory or its geographical location. Hence it can reach any corner of the world for you and me to see and interact. The Digital Twin experience may be enhanced even more by bringing Augmented Reality (AR) into the picture. But this is a subject for another article.
Solid engineering design is the genesis of a successful Digital Twin experience. Digital Twin based engineering is the future of product development. Except that the future is already happening now.