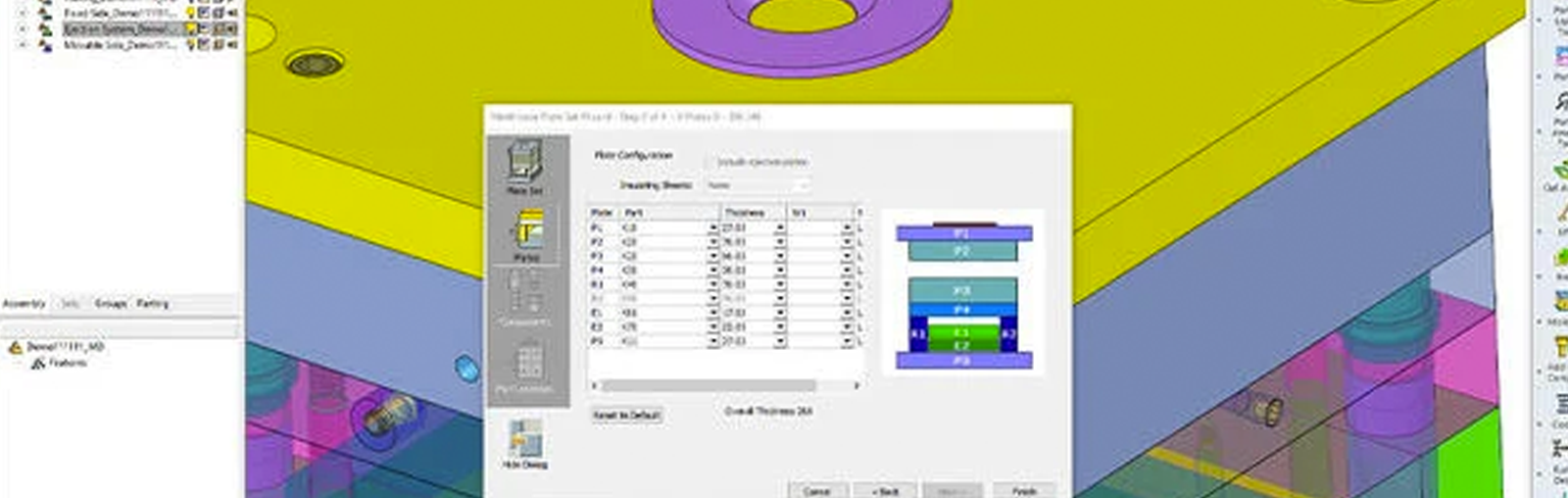
Four Productivity Strategies for Toolmakers during a Global Pandemic
Businesses are operating in an environment unlike anything most have experienced in their lifetime. The challenges placed in front of businesses by the global pandemic are highlighting the need for resilient business processes. Toolmakers who invest in the technology to support such processes are better equipped to withstand these challenges today and well positioned for the post-pandemic future.
To rise to the challenge, toolmakers can implement four productivity strategies.
Formalize internal knowledge to ensure consistency, quality, and speed.
While everyone is getting better at collaborating remotely, there is no substitution for face-to-face interaction between a designer and a CNC expert or a junior programmer where more-experienced teammates can quickly show less-experienced teammates how to do something with a few mouse clicks.
At times like this, it is imperative for toolmakers to turn their tooling software into a repository of their company’s knowledge and standards. Custom process templates that capture the knowledge of the best engineers are key to ensuring that toolmakers achieve the highest levels of quality and speed on any job, even at a time of social distancing.
Use any downtime to encode best practices into reusable standards and templates.
While toolmakers routinely recognize the need for process improvements, even the best intentions often take a back seat when everyone is busy delivering products and meeting deadlines. Toolmakers who see a slowdown in orders can use any downtime to prepare for the future by creating new templates and custom catalogs that would translate into speedier delivery and higher-quality standards when demand picks up.
Automate common toolmaking tasks with software that anticipates your next move.
Purpose-built software that automates routine toolmaking tasks can save valuable time, reduce errors, and allow users to focus their attention on tasks that demand greater attention. Designed with an understanding of the toolmaking process, intelligent automation anticipates the user’s next action and puts the right tool at the user’s disposal at the right time. These smart tools are especially useful when employees are working remotely in this global pandemic, as junior programmers don’t have company experts with them to help them.
Use concurrent engineering to streamline collaboration and accelerate delivery cycles.
Using integrated design and manufacturing software that allows NC work to get started while the design is still underway—and doing it safely without compromising part data integrity—can eliminate costly wait times. Toolmakers can compress delivery cycles further by allowing multiple designers to work simultaneously on the same project.
There is no denying that many toolmakers are facing challenges these days. At the same time, forward-thinking toolmakers can find opportunities for process improvements with benefits that will last long beyond the current global pandemic.
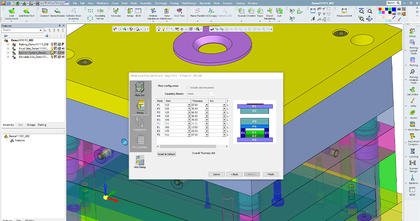
The Cimatron® mold base tool can generate endless mold combinations using standard and custom catalog parts—turning hours of work into minutes.
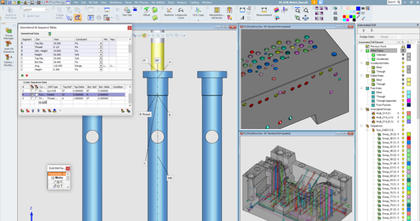
The Cimatron automated drill tool automates hole assignment to the appropriate drilling sequence—saving valuable time and eliminating errors.
Source https://3dsystems.com/