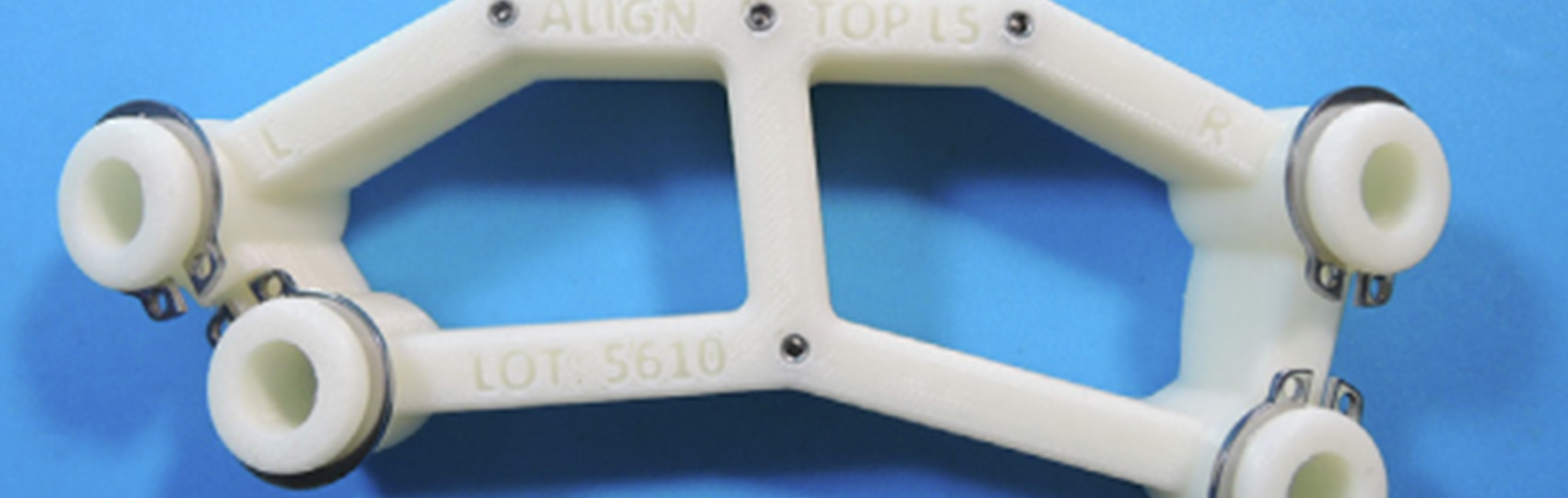
Anatomics Proves Viability Of 3d Printed Surgical Guides
Australian med-tech company Anatomics has conducted a study on the benefits of 3D printed patient-specific medical models for pre-surgical planning.
Using its 3D printed “SpineBox” kit to support spinal fusion surgery, Anatomics has measured the performance of the models on 129 patients, over a period of 27 months. These patients were all undergoing minimally invasive transforaminal lumbar interbody fusion (MIS TLIF) at a single centre, performed by the same surgeon. From the results, Anatomics has concluded that MIS TLIF represents a viable application for 3D printed patient-specific models, improving the efficiency and quality of the operation.
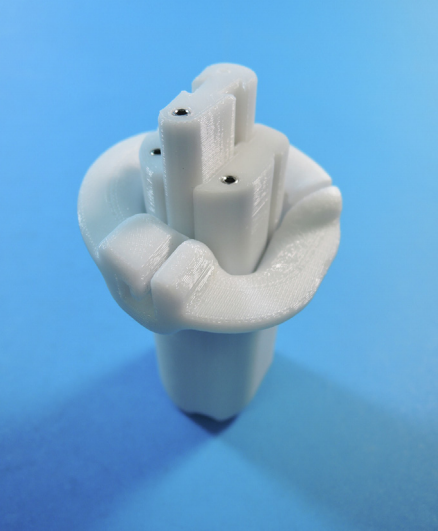
Patient-specific SpineBox tubular retractor and sequential tissue dilators. Photo via Journal of Clinical Neuroscience.
3D printed sternum implants
Based in Melbourne, Anatomics specializes in manufacturing and marketing surgical products to surgeons locally and internationally.
Working with Lab 22, the 3D printing service bureau arm of CSIRO (the Australian federal government agency for scientific research), Anatomics has 3D printed a number of medical implants over the years. In 2015 the company helped to design and 3D print a titanium sternum and rib implant for a 54-year-old patient in Spain, diagnosed with a chest wall sarcoma. Following this, again with Lab 22, it 3D printed a composite sternum and rib cage implant for a patient in the U.S. The implant was provided to a surgical team, led by Jeffrey L. Port of the New York-Presbyterian and Weill Cornell hospitals, who successfully performed the implant procedure on 20-year-old Penelope Heller.
Anatomic’s 3D printed sternum implant has also been implemented on a patient in the UK at Heartlands Hospital in Birmingham. The operation was the subject of a BBC TV series that aired in 2017 named “Trust Me, I’m a doctor,” which went on to inspire further 3D printed titanium implant procedures.
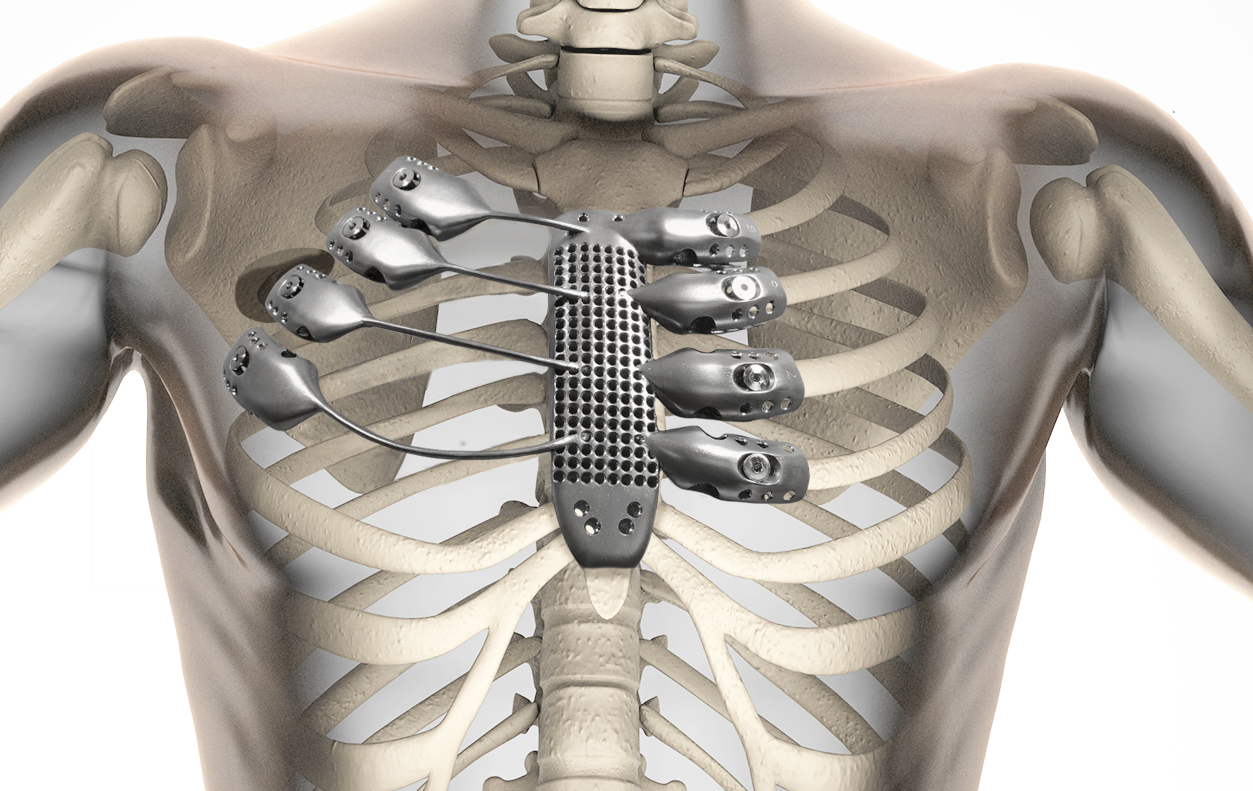
AnatomicsRx 3D printed metal rib cage. Photo via Anatomics.
How useful are 3D printed patient-specific models?
To carry out its study of surgical guides, Anatomics used patient imaging and surgical planning software to manufacture 3D printed patient-specific MIS TLIF kits for each of the 129 patients. These kits consisted of a 1:1 scale BioModel of the patient’s spine, stereotactic K-wire guide, osteotomy guide, and muscle retractors.
Each of the 3D printed spine models was used pre-operatively for surgical planning, patient consent, and education. Specifically, the BioModels can support procedures such as nerve decompression, fusion cage implantation, and help to provide accurate completion of the spinal construct.
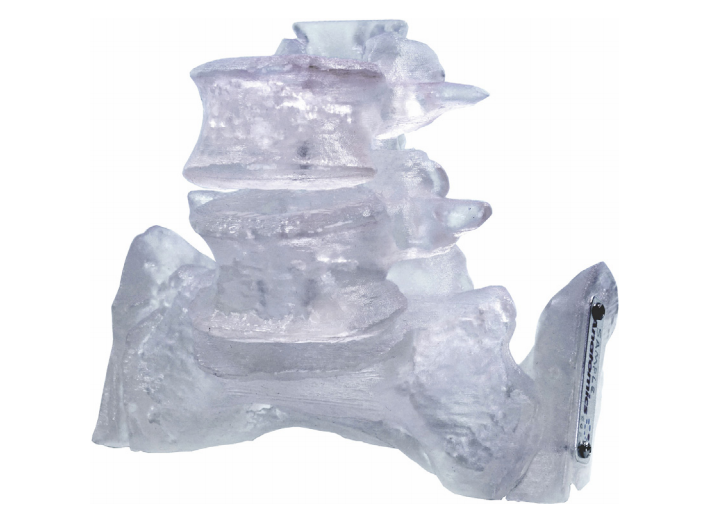
The 1:1 scale BioModel. Photo via Journal of Clinical Neuroscience.