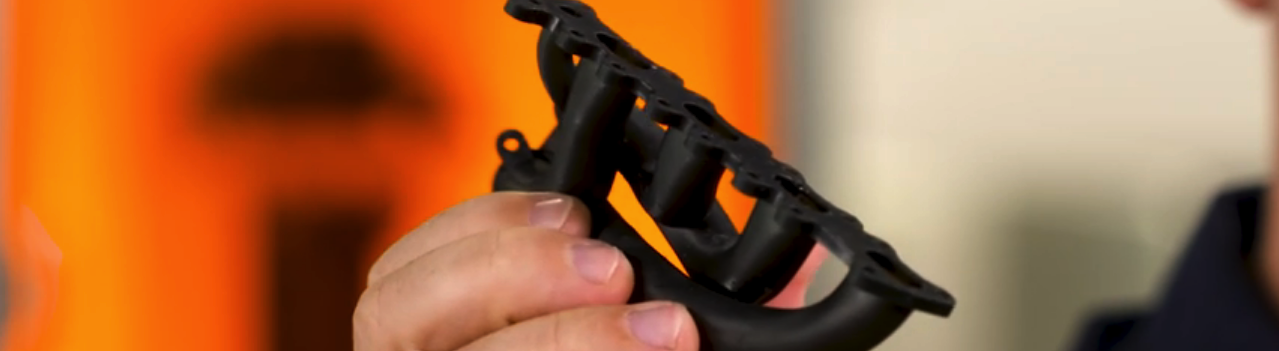
Figure 4 Today: Prototyping
BY: SAM GREEN
Welcome to the fourth installment of our 3D printing materials series. I’m following up on Jeff’s post about Figure 4 for production applications to share the advancements we have made in materials for prototyping. Whereas Jeff focused on the expanding opportunities for direct digital production, I am eager to let you know about how we are making prototyping more robust to continue helping you improve your product development process and experience.
As you may know, 3D printing has its origins as a prototyping technology, offering the ability to quickly produce accurate 3D models to accelerate design and development. If you think about it, there is probably not a single commercial or industrial product out there today that is not the outcome of multiple rounds of prototyping, testing, evaluation, and redesign. We therefore have our work cut out for us from a materials standpoint to deliver the widest prototyping material options to suit the widest array of possible applications and use cases.
Better material properties make better prototypes
Jeff already reviewed how the speed and quality of Figure 4 printing make it an amazing tool for the production floor. These attributes, as well as relative cost-efficiency, also make it an incredible asset in the workshop environment to rapidly produce prototypes and drive product development forward. In the realm of prototyping, we have focused our energies on developing materials to answer a wide range of needs, including toughness, durability, biocompatibility, high temperature deflection, and elastomeric properties.
Based on the positive user feedback we’ve received thus far, I think you’ll be very happy with what we now have to show. I’ll touch on each new material in turn, but I encourage you to click through for more information on any that you think might be a match for your next project.
Simulate the look and feel of injection molded ABS with Figure 4 TOUGH-BLK 20.
Durable, tough prototyping materials
In keeping with our workhorse materials, I will start by introducing Figure 4 TOUGH-BLK 20. This material simulates the look and feel of injection molded ABS and is a great fit for high performance parts. Its superior surface finish and industry-leading long-term environmental stability make it a great choice for rapid design iteration, strong and functional test components, and even short-run manufacturing, when the specifications align with the project requirements.
Figure 4 FLEX-BLK 20 has the look and feel of production polypropylene.
Figure 4 FLEX-BLK 20 is another new material that is both durable and flexible with excellent overall shape retention. It is a fatigue-resistant black plastic with the look and feel of production polypropylene. Engineered for long-term environmental stability it’s also an excellent match for functional assemblies and prototypes, as well as enclosures and master patterns for molding.
Prototyping materials with high heat resistance & biocompatibility
Of course, a number of the new production-grade materials that Jeff introduced are also ideal for prototyping applications. In particular, Figure 4 MED-WHT 10 and MED-AMB 10, which are biocompatible and capable of withstanding high heat (they can be sterilized in an autoclave), which makes these great for medical applications as well as high-heat industrial applications.
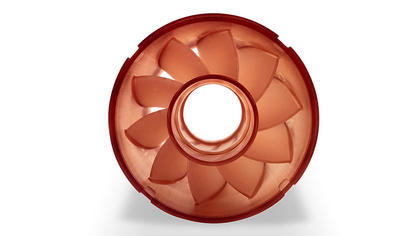
Figure 4 HI TEMP 300-AMB has an HDT over 300℃.
Rubber-like prototypes
For simulating soft-touch parts and end-of-arm tooling, Figure 4 RUBBER-BLK 10, is an exciting, malleable material for harder, rubber-like prototypes. This material is great for high performance functional and tough applications, such as grips, handles and bumpers, and provides a high tear strength and slow rebound. It’s also great for strain-relief applications, couplings and over molds.
Fast-tracking silicone parts
Last but not least, Figure 4 EGGSHELL-AMB 10 is an industry-first, and highly unique material optimized for sacrificial molds in silicone casting. It is specifically engineered to withstand liquid silicone injection at high temperature and pressure, while being easy to break away and remove following the casting process. The flexible manufacturing volumes enabled by Figure 4 make this machine and material combination a great option for batch silicone parts, whether for prototyping or production.
So there you have it! Many new materials, from tough and durable, to flexible and elastic, to some unique application-driven uses. We are really excited and proud to be expanding your capability to prototype for every stage of your product development process, whether its rapid concept models, highly detailed design verification prototypes, really tough parts for functional prototyping and even parts that will transition you into low volume production without missing a beat!
If you want more information on Figure 4 capabilities, I encourage you to download our white paper on same-day prototyping. As always, reach out to us with any questions. We’re more than happy to help.
Source https://3dsystems.com/